Your cart is currently empty!
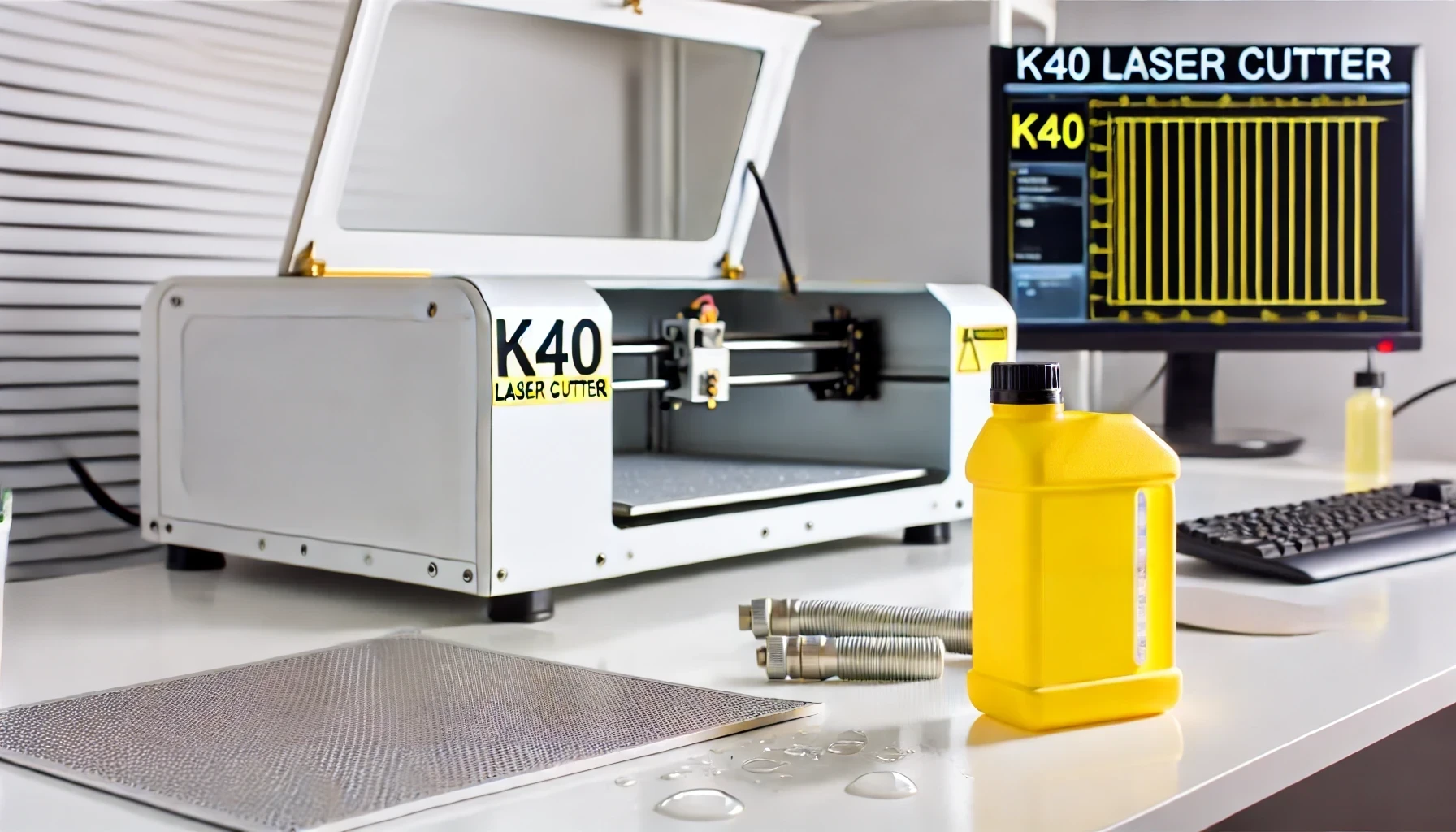
How to Switch to Yellow Antifreeze in Laser Cutters: Prevent Mold & Protect Your K40
Posted by:
|
On:
|
Switching from distilled water to a mixture of yellow antifreeze and water in your laser cooling system, such as for the K40, is a simple process but requires proper steps to ensure everything runs smoothly.
Step 1: Drain the Current Water System
- Turn off the laser cutter and disconnect the water pump.
- Drain the distilled water from the cooling system. Be sure to drain both the tubing and the reservoir. If there are visible signs of mold or algae in the tubing, consider running a cleaning solution (such as a diluted vinegar solution) through the system to flush out any residue.
- Clean the water tank or bucket used for the cooling system, making sure there’s no debris or buildup left.
Step 2: Inspect and Clean the Tubing
- While the system is drained, check the tubing for any visible signs of wear, mold, or blockages.
- If necessary, use a cleaning brush or pipe cleaner to carefully clean out the tubing to prevent any remaining mold or particles from affecting the new antifreeze mixture.
- Make sure the tubes are completely free of water before adding the new mixture.
Step 3: Prepare Your Antifreeze Solution
- Use yellow automotive antifreeze that is safe for aluminum and metals to protect your cooling system components from corrosion.
- Mix the antifreeze with distilled water in a 50/50 ratio. The distilled water helps to dilute the antifreeze, improving heat transfer efficiency, while the antifreeze provides protection from freezing, corrosion, and mold growth.
- Important: Always use distilled water—not tap water—as it prevents mineral deposits that can damage your system over time.
Step 4: Fill the System with Antifreeze Solution
- Slowly pour the mixed solution into your cooling system’s water reservoir. Ensure there’s enough fluid to circulate through the laser tube and tubing without leaving air pockets.
- If your system has a fill line, make sure the antifreeze solution reaches it. It’s essential to have enough fluid to keep the laser tube cool during operation.
Step 5: Prime the Pump and Check for Leaks
- Once the antifreeze solution is added, reconnect the water pump and prime it by turning it on and allowing the mixture to circulate through the system.
- Check the tubing and laser tube for air bubbles, which can prevent effective cooling. If you see any bubbles, gently tilt the machine or tubing to release them.
- Inspect the system for leaks. If any connections appear to be loose, tighten them before proceeding.
Step 6: Monitor Temperature and Performance
- Turn the laser cutter back on and run a test job while monitoring the temperature of the cooling system. The antifreeze solution should regulate the temperature effectively without overheating.
- After the test, check the system to ensure there are no blockages, and that the fluid is circulating evenly.
Maintaining Your Antifreeze Cooling System
Now that you’ve switched to antifreeze, it’s important to maintain the system to ensure optimal performance:
- Check fluid levels regularly to ensure the mixture stays at the appropriate fill line, and top off with the same 50/50 antifreeze and distilled water mix as needed.
- Flush and replace the antifreeze solution every 6 to 12 months. Over time, the antifreeze can break down, reducing its effectiveness in preventing mold and corrosion.
- Monitor tubing and fittings for signs of wear or mold. While antifreeze helps prevent biological growth, keeping an eye on the system’s health will help you spot any potential issues early.
Why Switch to Yellow Antifreeze?
Using antifreeze instead of plain distilled water offers several key benefits:
- Prevents mold and algae: The biocides in antifreeze kill off any potential growth of mold or algae in your system.
- Corrosion protection: Antifreeze contains inhibitors that prevent corrosion of metal parts, extending the life of your laser tube and components.
- Freezing protection: For those in colder climates, antifreeze helps prevent the water from freezing, which can cause damage to your laser cutter.
- Easy maintenance: With antifreeze in your system, you can go longer between fluid changes compared to plain distilled water.
By following these steps, you can ensure a smooth transition from using distilled water to yellow antifreeze in your K40 or other laser machines. This switch not only prevents common issues like mold but also extends the lifespan of your machine by protecting against freezing and corrosion.
For more tips and designs for your laser cutting projects, don’t forget to check out Mountaineer Tradepost for a variety of ready-made SVG files optimized for laser engraving and cutting!
Leave a Reply